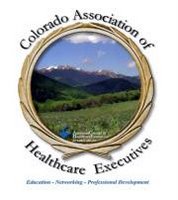
One of the topics was "Using Lean Principles to Optimize Workflow and Quality in Cardiology Care". The speaker mentioned Deming (same guy that my statistics teacher had us read a book about). Basically, the talk was regarding applying Industrial Engineering concepts to healthcare (without calling them that). I spoke with him afterwards because I am still trying to figure out why the healthcare industry hasn't caught on to the basic concepts that most businesses have been doing for 20 years. I suggested my theory that even though there are plenty of people with their MBAs in the hospital, most of them have medical undergrad degrees or backgrounds. They get their MBAs but never leave healthcare, so they don't see it implemented in the real world and have a hard time doing it themselves. He agreed with me and encouraged me that my educational background and prior work experience could be very valuable if I continue in the field.
I'm just trying to figure out who's really running the show and what leadership position I would need to be in to make a difference. Plenty of hospitals have Process Improvement or Quality teams/departments. Even the hospital I'm at has one. They make departments choose a Performance Improvement project. I even get solicited from RNs that want to use the EMR to help them on a improvement project, so they can get a certification. To me, it is just like Bob Nardelli trying to bring Six Sigma to Home Depot. There is a group dedicated to Six Sigma. They all have their black-belts and guide those working on Six Sigma projects throughout the company; however, from my perspective few of the projects seemed to be completed. I'm guessing perhaps people got a little busy working until 4am on a Sunday preparing for a quarterly earnings call. There is a similarity in these examples, and it's that the leadership perhaps likes the idea and thinks it should be happening, but ultimately it is not a priority.
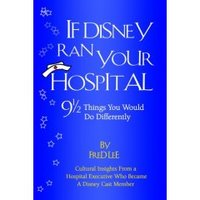
He also mentioned to me that he thought healthcare was about 5 years behind getting traction on these ideas. He made a distinction between "lean" concepts and something like "Six Sigma". He said most companies implementing Six Sigma have already gone through the lean process. They are starting out with somewhat trimmed down, lean processes. The Six Sigma method then improves these. The lean concept focuses on "Plan, Do, Check, Act" (the Deming cycle). He thought most hospitals had problems with the "check" and "act" part of the process. He had to get help from an outside source when trying to implement changes in his own hospital because he didn't have the experience or education to do it himself. I've seen at my current work that people are asked to do things they have no experience in and are given no guidance. Often, there are good ideas but they get lost in poor execution. That's an interesting topic "poor execution". I saw it demonstrated at Home Depot and now the hospital. There is a book on the topic, perhaps my next read.